The Covid-19 pandemic is a constantly evolving crisis. The pressures on the already over-stretched and under-resourced NHS are more apparent now than ever before.
In response to the critical shortage of medical devices such as ventilators that will be required to treat serious cases of the virus and other life-threatening conditions, the government has turned to the manufacturing industry for urgent assistance. On Sunday, the Health Secretary Matt Hancock announced that the government is now seeking support from engineering and other manufacturing firms to switch their production processes to the manufacture of additional devices for the NHS. A helpline has been set up through which firms can offer their services to the government.
Many have pointed out that, in the absence of sufficient numbers of NHS staff, additional ventilators and other devices could not be administered in any event. There are also issues surrounding the supply of the component materials to produce the equipment required. This is not the only potential roadblock to the plan for mass-manufacture solving the issue.
Regulation of medical devices
Regulation of medical devices in the UK places a number of requirements on companies wishing to bring devices such as ventilators onto the market. Any company offering its services should be aware of the potential obligations that it will be subject to by undertaking this work.
ISO 9001 is an international generic quality management standard for the manufacture of all products. Manufacturers will already be familiar with this. However, medical devices fall under an expanded framework (ISO 13485), which is specifically designed for medical device manufacturers, and any such products must conform to this standard before entry to the market.
The Medicines and Healthcare products Regulatory Agency (“MHRA”) regulates medical devices in the UK. The framework for placing these devices on the market is governed by the Medical Devices Directive, and from 26 May 2020, the new Medical Device Regulations. These operate to ensure that medical devices meet the required standards for patient safety, and suitability for their intended purpose.
Under the regulatory framework, medical devices are given a classification based on the level of risk associated with using them. Class I products can be placed on the market without further assessment, whereas strict controls are applied to Class III products which attract a higher level of risk. Ventilators are categorised as Class II medical devices. This means that they must be approved by a notified body (designated by the MHRA to assess compliance) who will carry out a conformity assessment for the product. Amongst other things, this will include a review of manufacturing processes and quality management systems in order to ensure that the manufacturer of the device in question complies with the regulations. This process can take many weeks, depending on the complexity of the device. Once satisfied, the notified body will issue a CE certificate which indicates conformity with the regulations. At this point, the product may be put on the market.
Manufacturer obligations
Once on the market, the manufacturer is under an obligation to ensure the long-term safety of the device. This includes undertaking post-market surveillance and reporting serious incidents involving their products to the MHRA. The MHRA also has ongoing powers that include attending premises to inspect products, manufacturing processes and testing arrangements.
Suffice to say that the obligations on manufacturers involved in making these products are not straightforward. If the manufacture of additional ventilators can genuinely assist the NHS in coping with the strain of Covid-19, emergency exemptions to the current framework may be brought in to encourage manufacturers with the relevant capabilities to come forward.
These specific requirements are in addition to other legal issues which companies embarking on this work should consider, including insurance, licensing, employee safety standards for medical device manufacture, and the impact on their ability to fulfil existing customer contracts.
For a discussion on what questions your business might have to consider in relation to any of the issues discussed here, and generally in relation to Covid-19, please contact us.
Written by
Related News, Insights & Events
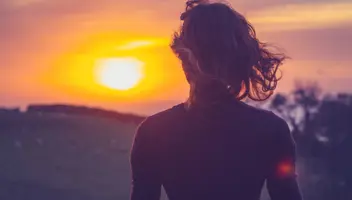
Navigating legal and compliance challenges in the energy sector: from environmental risks to workforce management
01/10/2025 - The Marcliffe Hotel (N Deeside Rd, Pitfodels, Aberdeen AB15 9YA)
Navigating legal and compliance challenges in the energy sector conference - we will cover environmental risks to workforce management
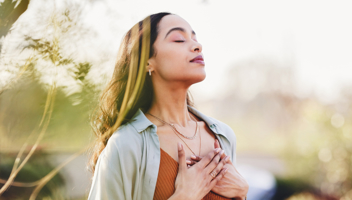
Women's Health Showcase with the Scottish Lifesciences Association
11/09/2025
We’re partnering with the Scottish Lifesciences Association (SLA) to once again showcase some of the cutting-edge Scottish life sciences companies working to improve women’s health.
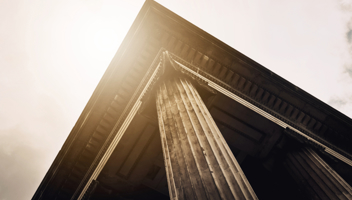
The 2019 Hague Convention: a case to litigate, instead of arbitrate, cross-border disputes?
This insight explores the 2019 Hague Convention, in force in the UK from 1 July 2025, and what it means for cross-border enforcement of court judgments.